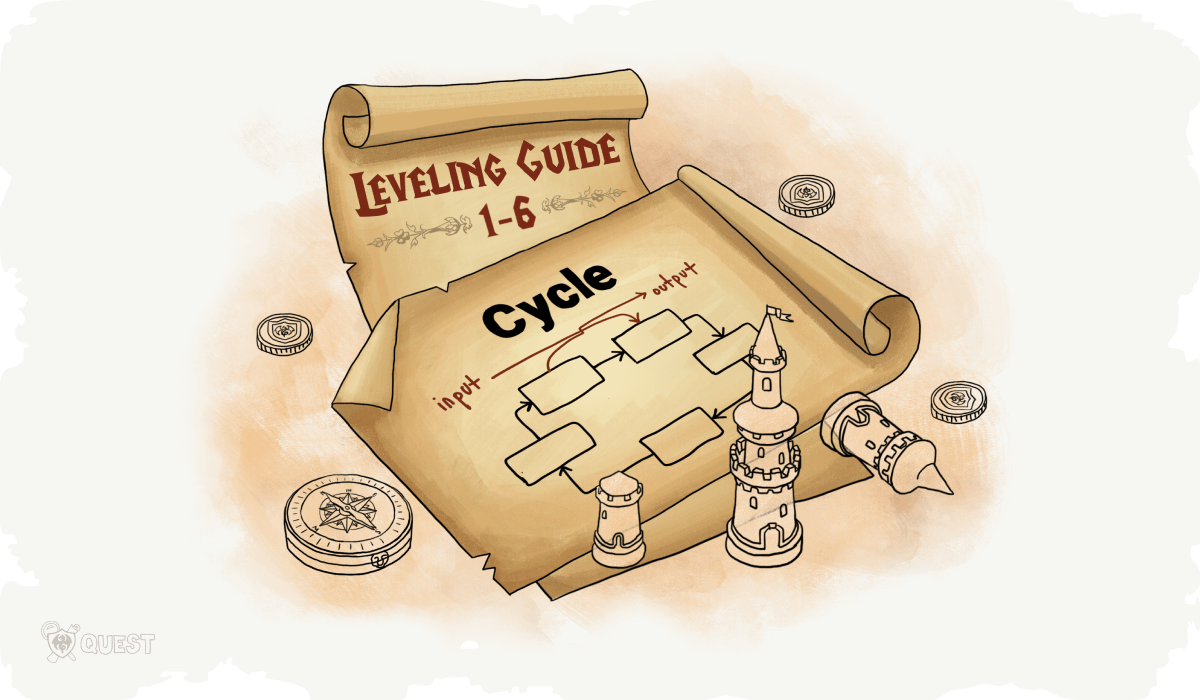
cycle architecture is a chain that repeats, usually with a standardized periodicity. When a new cycle begins, the process receives the new inputs and in some cases may partially use the outputs of the previous cycle of operations.
Examples: day-to-day operations of hotels and hospitals, railways and airlines, and banks and museums; regular management processes: PDCA, HADI, Build-Measure-Learn cycles, and monitoring processes.
Research landscape of the Cycle
There are three main research spaces to be explored: Gears, Assets, and Schedules.
Gears
Cyclic processes do not exist isolated — most likely there are connected loops made up of the cycles that supply the inputs or consume the outputs, larger and longer cycles that maintain and control our cycle, or even shorter and faster auxiliary cycles that perform shorter subtasks. Cycles and chains work together. Quite frequently, they are building blocks for larger chains, funnels, or bigger cycles, wherein the step of a larger process is actually a small cycle. So the cycle may be considered as an individual gear in a large mechanism.
Inversely, smaller chains and funnels can be supervised by a large cycle, just like factory managers recurrently (cycle) supervise and coordinate multiple production lines (assembly chains).
There are usually of three types of cycles:
- Queue processor: This cycle has a clear beginning and the end, which makes it similar to a simple chain. After completing all the steps, the system takes the next input item from the external queue and repeats this process again.
- Continuous processor: The system repeats the steps without clear starting and ending points. Some steps may have inputs, others may generate outputs.
- Process initiator: This one does not have any specific work item as an input, but instead by executing their steps an it can initiate a new work chain that will trigger a sequence of other chains and cycles.
Examples of a queue processor: a hotel accommodates the guests for the night and welcomes new guests the next day, a customer service agent receives calls and assists customers, and a pasteurizer machine receives bottles from the conveyor belt.
Examples of a continuous processor: a thermostat maintains the temperature and humidity of the house, a bus moves around the city along its circular route, and an old lighthouse shines in the night to help navigate hazardous coastlines.
Examples of a process initiator: an executive committee defines the high priority projects for the next year, a police officer on duty receives a call about a bank robbery, and a regular inspection identifies that a car requires repair. These cyclic processes (committee meetings, police duty, and car inspection) may generate an event that starts a new process, a sequence of actions.
When mapping this space of the research landscape, you should not just lay out the steps of the specific cyclic process, but also explore what other chains and cycles are involved. In fact, you should identify the main gears of the larger mechanism.
Assets
Like the other chains, cycles also require tools, resources, and other assets to be functional. These resources may be involved in different steps of the cycle or event to different cycles of a larger process. Some assets are critical and can easily become a bottleneck of the whole mechanism. To properly serve, the assets require attention, recruiting, preparation and maintenance. Understanding the current landscape of the assets may help you identify bottlenecks and other potential issues in the cyclic process.
Examples of assets: trains for a railway company, trees in a fruit farm, operating rooms and nurses at the hospital, and top managers in an executive committee.
Schedules
As long as it is a cyclic process with multiple repetitions, we need to take care about both short-term and long-term availability of the assets. The system runs through hundreds of cycles, so the tools and resources must be available and in good shape. If the demand grows and higher throughput of the cycle is required, more tools and labor must be employed. If demand drops down, the tools must be reset for other functions.
Thus, there are two more areas to explore: long-term planning and short-term scheduling.
- Planning is responsible for the long-term allocation of the resources and coordination of the cycles as a reaction to the external demand during the next months or years. Plans define what types of items will be processed at what forecasted volumes, what assets should be allocated, and how much additional resources may be required.
- Scheduling is responsible for the short-term allocation of individual assets during the upcoming hours, days, weeks, or months. Schedules employ and coordinate the assets that were allocated by previous planning.
Examples: planning of the volumes of cars to be manufactured for the next year and scheduling of workers and machine tools for the next week and planning of classes for the next university year and scheduling of the professor work hours and lecture halls for the next semester.
Researching this space, you may find serious inefficiencies and bottlenecks. By eliminating them, the general efficiency of the cycles may be considerably improved.
Problem analysis
The main four problems in the cycle are usually:
- Overload and long queues on critical assets, critical cycles and shortage of critical supplies that cause the consequent delays, and empty queues and idle time on the other assets and cycles
- Low throughput of the system due to desynchronization of cycles
- Cycles that are too long to keep up with the evolving external demand
- Effectiveness and cost of the processing on each step as in any other chain
A multi-cycle system can be extremely efficient and lean if every gear of the mechanism is matched and synchronized. One way or another, any mature system of processes begins to look like a design of well-coordinated cycles and chains.
However, before that, the system of cycles undergoes a long evolution. Cycles do not just need to be designed and matched accordingly but also be aligned with the external demand that pushes the items or requests into the system. Demand volume may have peaks, fluctuations, or other aperiodic patterns. Such inconveniences complexify the design of a flexible and efficient mechanism.
Similarly to the assembly chain it is important to understand the criticalsteps, subcycles, assets, or supplies that jam shut the whole system. When one gear is blocked, the others suffer. That means that the remedy is usually in redistributing the load, allocating more resources or rescheduling. When the blockade is caused by critical supplies, explore whether the supply chaincan be reworked.
When you feel the gears are not well connected and synchronized, review the cycle time for the connected cycles. The gears work best together when their cycle time is coherent. For example, in management, the project team may have daily cycles for internal sync, weekly sync with the customer, and monthly sync with their management. The meetings with different stakeholders scheduled in the calendar look just like the footprints of the mechanical gear teeth, and these regular meetings drag the project forward just like the mechanical gears drag each other and make the machine move.
In case of fluctuating external demand, it is usually recommended to shorten the planning cycles. For example, reduce the period from yearly to quarterly planning, or from quarterly to monthly or weekly. Such changes may be uncomfortable as they incline the accustomed ways of doing business, however they may be the only way to survive.
Common flaws and illnesses of a cycle:
- Low throughput of the system of cycles
- Desynchronization of the cycles
- Overload and underutilization of the assets
- Expensive processing or ingredients
- High failure/defect/waste rate
- Poor availability, condition or conflicts in usage of assets
- Inventory shortages or overstocking
- Expensive idle time
- Too much unfinished work in progress
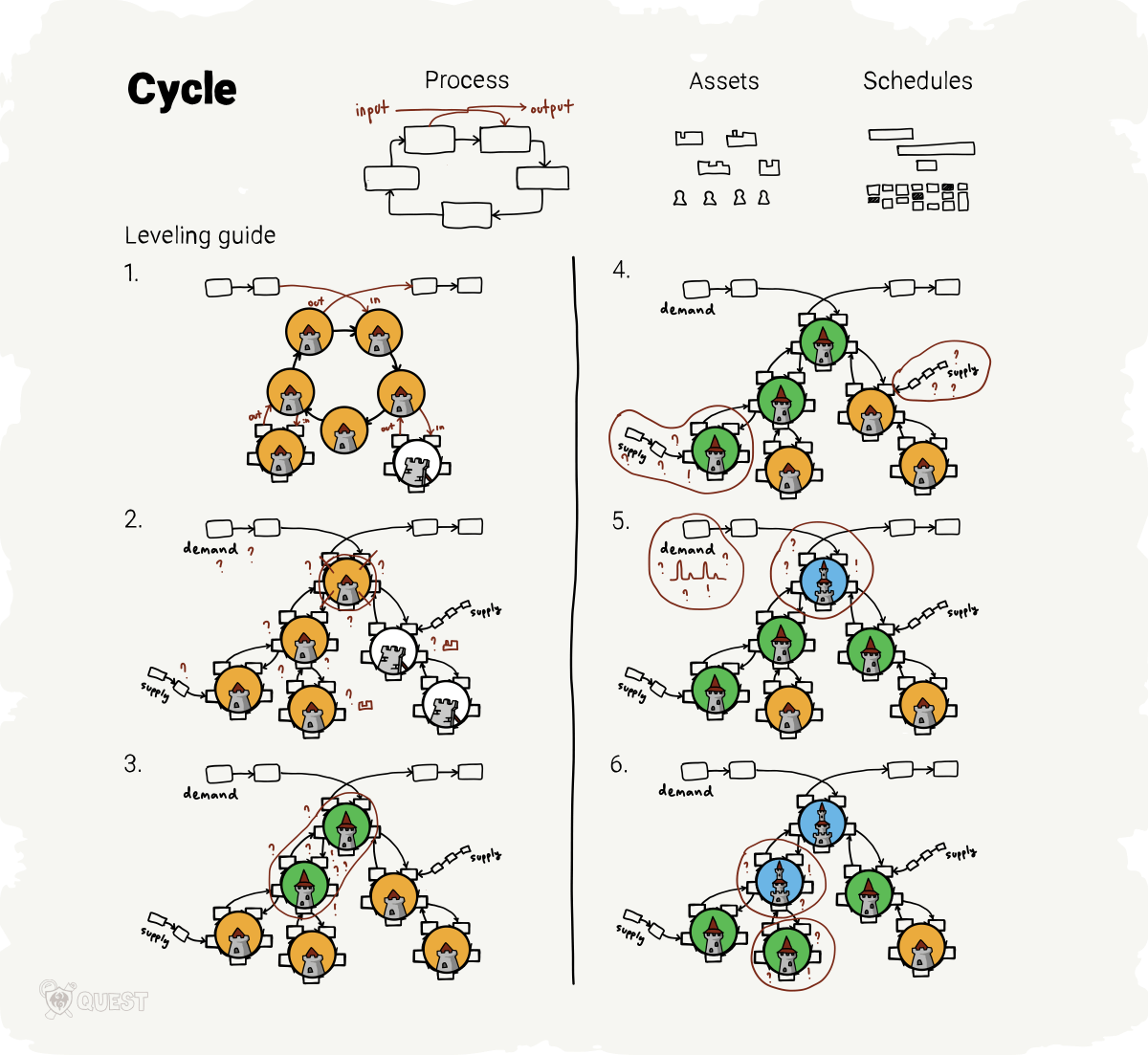
Leveling guide — Cycle
If you’re designing and building a process from scratch:
Create Placeholders of all steps of the cycle and the system of cycles, then upgrade them to the Quick & Dirty level (Low Fidelity, Medium Quality). Create simplified schedules without trying to over-optimize the system. Try to have dedicated assets for every cycle and avoid sharing one asset between several cycles. Such a system may be expensive and not economically viable, but your goal is to start the ball rolling and you will optimize it in the next phases.
If you’re improving an existing process, skip phase 1 and go to the next phase.
Target discovery: identify the reasons of blockade in the cycle: overload of critical cycles or assets, shortage of critical supplies, or irregular demand.
Experiment with the reengineering of critical gears and upgrade to Good Enough level: try to reschedule the usage of critical assets, adjust the cycle time, add new gears if necessary.
Identify the shortage of critical supplies, try to schedule them better or understand if the supply chains may be reengineered.
Analyze the demand patterns, introduce new planning techniques, reduce the planning cycle time, and adjust the schedules. Identify the need for adding or outsourcing assets and resources to reflect the changing demand.
Continue identifying hindrances in the cycles. Further upgrade the gears to Good Enough and the most important ones to State of the Art level.
Always evaluate not just improvement of the individual gears, but also the performance of the system as a whole.